JSEDM Wi-50E: High-Precision Flush-Type Wire Cut EDM Machine with 500/300/300 XYZ Travel
JSEDM's Wi-50E Flush-Type Wire Cut EDM features 500/300/300mm XYZ travel with high-precision 5-axis servo control. Designed for mold manufacturing, automotive parts, and precision machining with advanced three-body structure, user-friendly 15-inch touchscreen interface, and rapid wire threading system. Perfect balance of performance and cost-efficiency.
Flush-Type Wire Cut EDM XYZ Travel: 500 / 300 / 300
Wi-50E
Flush-Type Slow Feeding Wire Cut EDM
Both the Wi-50E and Wi-30E are flushing-type wire EDM machines, but the Wi-50E has the same travel range as the submerged-type Wi-530S, offering a larger machining area and greater flexibility. The Wi-50E is a high-performance wire EDM machine with excellent machining capability and precision. The machine features a flushing-type design, which helps to keep both the workpiece and the cutting wire clean during the cutting process. Additionally, the machine is equipped with high-quality components such as PMI brand ball screws and linear guides, as well as driver and servo motors made by Delta Electronics, ensuring high precision and stable machining.
Machine Introduction
The Wi-50E features a travel range of 500mm on the X-axis, 300mm on the Y-axis, 300mm on the Z-axis, 100mm on the U-axis, and 100mm on the V-axis, making it a high-performance, versatile use wire EDM machine. It is suitable for various manufacturers and applications, meeting the demands of high-precision machining, enhancing production efficiency, and improving product quality. Additionally, the user-friendly interface makes it easy to operate, catering to all types of users, from beginners to experienced operators.
Below are the several features of Wi-50E:
- The Wi-50E is suitable for cutting workpieces with thicknesses ranging from 30mm to 70mm, such as automotive parts, mold manufacturing, and tool and die processing. When the upper and lower heads are aligned with the workpiece using the water jet covers, the cutting speed and precision are identical to those of the Wi-530S.
- The Wi-50E can be used for mold design and prototyping, and its low cost combined with high performance makes it an ideal choice for startups or product development.
- The Wi-50E is well-suited for use in educational and training institutions, allowing students to learn wire-cutting techniques. Its simple operation makes it ideal for teaching and practical training.
- The Wi-50E is designed with a system that allows for quick and easy replacement of consumables, saving both operation time and costs.
High-Rigidity Structure:
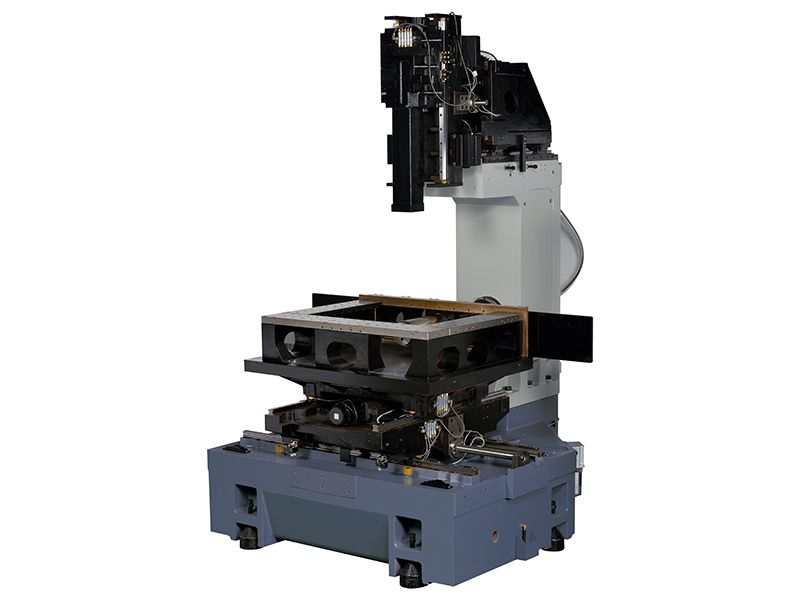
- The machine body utilizes CAE (Computer-Aided Engineering) to simulate structural deformation of each axis during actual operation. Therefore, we use a high-rigidity T-shaped machine body structure to reduce load and thermal deformation issues, ensuring permanent mechanical accuracy.
- Casting was made from Meehanite cast iron, stress-relieved through heat treatment, it features a high-rigidity, symmetrically balanced design to reduce load and thermal deformation.
- The overall transmission structure employs a high-power AC (400W) servo motor, paired with Taiwan's PMI ball screw and linear guides, this combination greatly reduces rotational errors. And with the adjustment of pitch compensation and backlash compensation in the control system, it ensures the precision of the machine's movement.
High-Precision Drive Shaft System:
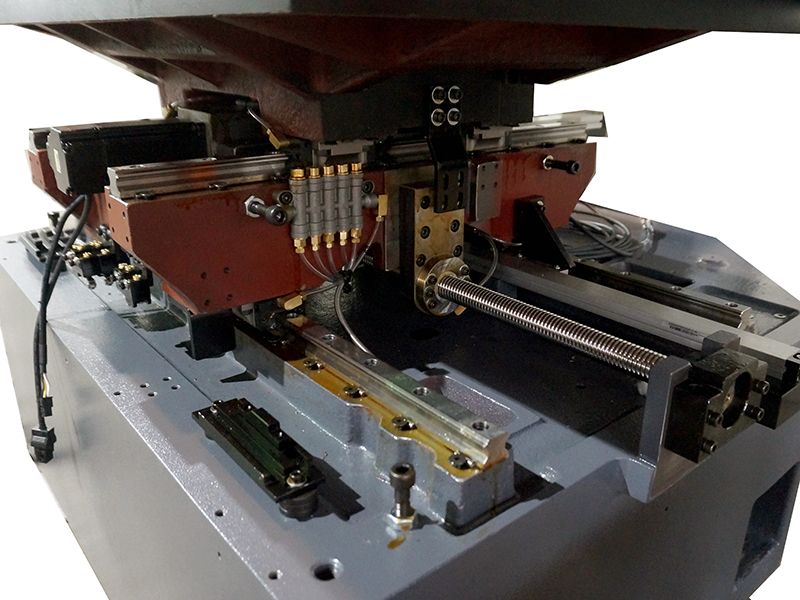
The drive shaft uses highly precise "double nut" ball screws to achieve high rigidity, smooth operation, and minimal lead error. It is equipped with a high-torque, high-response AC (400W) servo motor, with an optional Fagor high-resolution optical scale for full closed-loop control. The optical scales are installed as close to the ball screws as possible, ensuring each axis maintains high precision, long life, and excellent stability.
Self-developed Wire Delivery System:
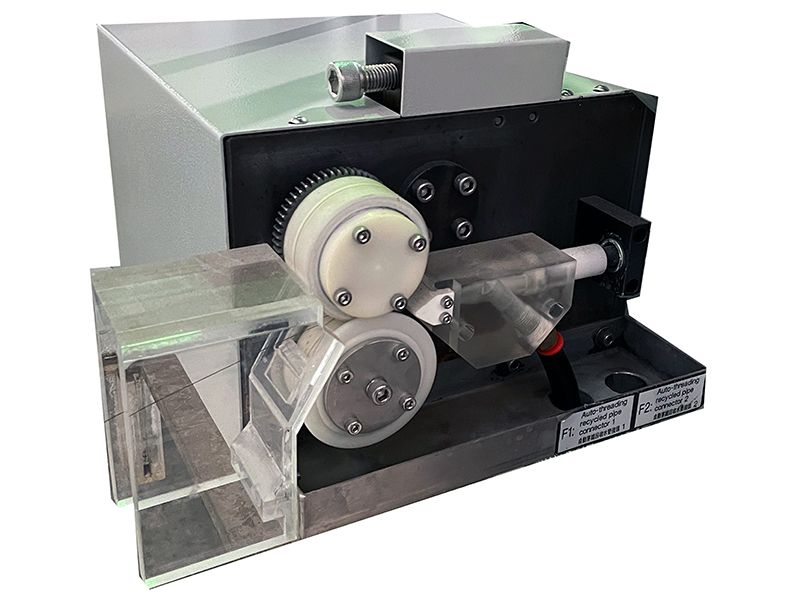
- The special structural design, combine with high-hardness ceramic pully, results in less wear and longer lifespan.
- With Japanese Panasonic AC servo motors, magnetic powder clutches, wire collection motors, and wire clamping mechanisms, the system can accurately make adjustment for instability caused by wire vibrations, ensuring stable wire delivery and low failure rates.
- The wire delivery system uses advanced constant tension motors for copper wire, it assures tension stability at all times and prevent copper wire entanglement caused by sudden breaks during normal operation.
- The wire delivery section utilizes a conduit-style collection structure. During threading, high-pressure fluid flow guides the copper wire to complete the threading process quickly within 3-5 seconds. Additionally, the use of high-quality ceramic wheel mechanisms ensures minimal wear over long-term use, eliminating the need for additional parts. Even ∅0.1mm copper wire can pass through easily without tangling.
Controller Performance and Features
● Right-angle Compensation: This function compensates the right-angle and parallelism of the XY and UV planes of the wire cutting machine. After compensation, the machine's right-angle accuracy can reach within ±1.5μm/300mm.
● Five Types of Corner Assist Lines: Contains additional corner assist line functions compared to other wire cutting machines:
0 - Intersection point
1 - <90 degrees (tangent) => Additional function
2 - <90 degrees (arc) => Additional function
3 - Tangent => Additional function
4 - Arc => Additional function
● Fuzzy G95 Control: Achieves more than 95% of manual operation speed, or even better.
● 212 Sets of Ultra-fine Machining Parameters: Provide 212 sets of ultra-fine machining parameters that can be adjusted according to different cutting needs.
● 10 Sets of Arc Deceleration Machining Parameters: Automatically switches machining parameters according to the arc radius set by the user.
● 10 Sets of Corner Deceleration Machining Parameters: Automatically switches machining parameters according to the corner angle set by the user.
● Ethernet Access Interface: Provides an Ethernet interface for accessing large amounts of machining data.
● 100 Sets of Coordinate System Records (Including G54 ~ G59): Traditional wire cutting systems only provide 6 sets of coordinate records (G54 ~ G59). JSEDM Wire Cutting System offers up to 100 sets of coordinate system records, which can be used for positioning movements.
● Dynamic 3D Graphical Display: Simulates graphics in 3D and allows zooming, regional enlargement, and rotation for detailed viewing.
● Touch Operation Interface: Uses a 15-inch high-resolution industrial-grade touch screen with an intuitive interface, significantly reducing operator learning time.
● Simple Operation Interface: Compared to the traditional DOS multi-layer operation menu, the Wire Cutting System simplifies the operation interface significantly and adds a hotkey area to centralize commonly used function keys, effectively reducing learning time and operation difficulty.
● Simplified Calibration Steps: Most functions only require 2-3 steps to start the calibration process, this simplifies the operation flow and shortening calibration time.
● Maintenance Information: Records six types of maintenance information, timely reminding the operator to replace consumables. The maintenance information includes: 1. Copper wire usage length, 2. Waste wire bucket usage time, 3. Water tank filter usage time, 4. Electron feeder usage time, 5. Ion exchange resin usage time, 6. Workbench usage time.
● POS Function: When this function is activated during machining, it automatically speeds up the machine when the workpiece is not in its path and resumes the machining speed once it touches the workpiece and cutting starts. This function greatly reduces machining time.
Product Specification
Technical Spec. | |||
---|---|---|---|
Machine Type | Flushing | Drivetrain | 5 axis AC servo system |
Mechanical Structure | Three-Body Independent | Simulations Axis | XYUV (4 axis) |
Max. Workpiece Size L x W x H (mm) | 870 x 520 x 295mm | Wire Diameter Range | Φ 0.10 ~ 0.3mm |
Max. Workpiece Weight | 700kgs | Max. Taper Angle | ± 22.5° (Thickness 100mm) |
X Axis Travel (Right-Left) | 500mm | Max. Axis Load | 10kgs |
Y Axis Travel (Front-Back) | 300mm | Conductivity | Automatic |
Z Axis Travel | 300mm | Water Tank Capacity | 270L |
U Axis Travel | 100mm | Dimension ( W x D x H) | 2600 x 2200 x 2150mm |
V Axis Travel | 100mm |
- Gallery
- 2.5D image simulation allows customers to easily track the current cutting status, especially in taper cutting and abnormal shape with upper-lower shape difference.
- Multi-functional calibration interface equipped with graphical explanations, making it easy for users to learn and operate.
- Time-based maintenance records enable customers to replace consumables at routine time, enhancing machining stability.
- Time-based maintenance records enable customers to replace consumables at routine time, enhancing machining stability.
- With machining parameter data sheet, customers can refer to built-in parameters and select suitable machining conditions based on wire diameter, number of machining passes, and material type.
How Does the Wi-50E's Three-Body Structure Improve Mold Manufacturing Precision?
The Wi-50E's innovative three-body independent structure, crafted from stress-relieved Meehanite cast iron, dramatically reduces thermal deformation and maintains mechanical accuracy during extended mold cutting operations. This design, combined with CAE-simulated structural optimization, delivers superior surface finishes within 0.01mm per 200mm at any position, allowing mold manufacturers to achieve complex geometries with exceptional precision while minimizing post-processing requirements. Contact us to learn how this structural advantage can elevate your mold production quality.
What distinguishes the Wi-50E is its intelligent control system with a user-friendly 15-inch touchscreen interface that simplifies operation while providing powerful functionality. The machine excels in both performance and practicality with its self-developed wire delivery system featuring high-hardness ceramic pulleys and constant tension motors that ensure stable wire feeding and minimal wear. With capabilities including right-angle compensation within ±1.5μm/300mm, 212 sets of ultra-fine machining parameters, and dynamic 3D graphical display, the Wi-50E offers an ideal balance of cutting-edge technology and cost-efficiency for manufacturers seeking to enhance production quality while maintaining operational simplicity.