JSEDM EB606N: Moving Table-Type ZNC EDM Machine with 400/300/180 XYZ Travel for Precision Mold Making
JSEDM's EB606N Moving Table-Type ZNC EDM offers 400/300/180mm XYZ travel with high-precision ball screws for small mold manufacturing. This economical EDM machine features AI automatic indexing, user-friendly interface, and multifunctional calibration, delivering excellent machining performance for mold cores and precision components with minimal electrode wear.
Moving Table-Type ZNC EDM XYZ Travel 400 / 300 / 180
ZNC-EB606N
Moving Table-Type ZNC Electrical Discharge Machine
The EB606N is an economical ZNC EDM machine specifically designed for machining small mold and small-size workpiece. Its XYZ axis are equipped with precision-grade lead screws, ensuring stable and vibration-free movement, thereby delivering high-quality machining results. This EDM machine is suitable for beginners or small factories, offering simple operation and high-efficiency machining capabilities. The EB606N is designed with a focus on accuracy and stability, meeting the machining needs of small molds and workpieces. It is a reliable and affordable EDM machine choice.
Machine Introduction
The EB606N is a multifunctional ZNC EDM machine, offering both flushing and submerged oil machining methods, allowing flexible selection based on different machining process. The XYZ axis of EB606N are equipped with precision-grade ball screws and 0.5µm optical scales, ensuring stability and accuracy during movement. With travel ranges of 400mm on the X-axis, 300mm on the Y-axis, 180mm on the Z-axis, and 250mm on the auxiliary axis, it is well-suited for small molds.
Below are the three relevant industries:
- Mold Core: While machining mold core, many molds are divided into several components for easier future maintenance. In such cases, the EB606N excels in repairing mold cores. Due to its smaller size, this machine reduces the initial investment cost. Combined with our company's EDM control technology, it can achieve the required precision and surface roughness for molds.
- Pipes used in Oil Extraction: The EB606N demonstrates outstanding performance in machining pipes used in oil extraction. These pipes require variously sized holes and ridges to be machined around the pipe walls. Using the manual rotary axis and high-energy discharge, the EB606N can complete these complex machining tasks in a short time. In this scenario, the EB606N showcases its flexible machining capabilities and high efficiency.
- Brand Logo Molds: Brand logo molds are typically smaller, the size of EB606N perfectly meets the machining needs. Many logo molds for well-known automobile brands are produced using EDM machines with the similar size as EB606N.
High-Rigidity Structure:
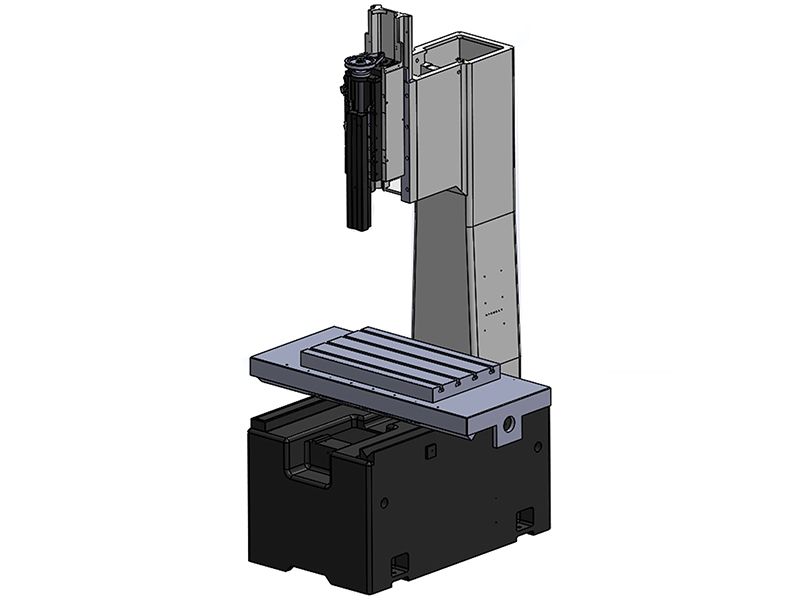
- The machine body structure utilizes CAE (Computer-Aided Engineering) to simulate structural analysis of each axis during actual operation. Therefore, we have adopted a high-rigidity T-shaped body structure to reduce load and thermal deformation issues, ensuring long-term precision of the machine.
- Made from Meehanite cast iron and stress-relieved through heat treatment, the structure features a high-rigidity, symmetrically balanced design, which helps reduce load and thermal deformation.
XY-Axis Travel Structure:
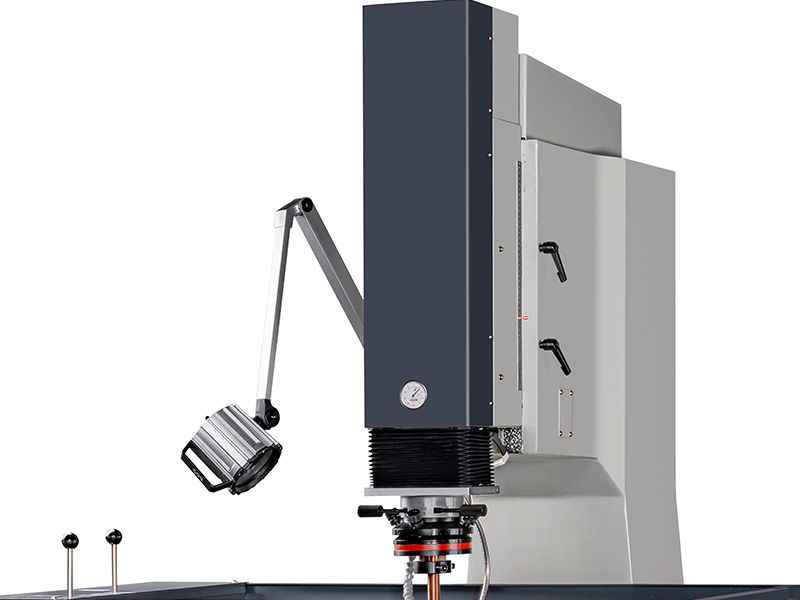
- The X and Y axis guideways are composed of a combination of V-shaped and flat structures, ensuring that the perpendicularity and parallelism remain unchanged over time. This structural design ensures that the EDM machine maintains excellent machining precision even during extended operation, with no changes in perpendicularity or parallelism, providing a stable foundation for machining tasks.
- The sliding contact surfaces of the X and Y axes are equipped with low-friction, wear-resistant plates (TURICE-B). These wear-resistant plates ensure precision and smooth operation under heavy loads. With a low coefficient of friction, they reduce frictional resistance while maintaining stable operation under heavy loads, ensuring machining accuracy and operational flexibility of the EDM machine. This design not only enhances operational comfort but also ensures machining precision and stability.
Z-Axis Structure and Precision Control:
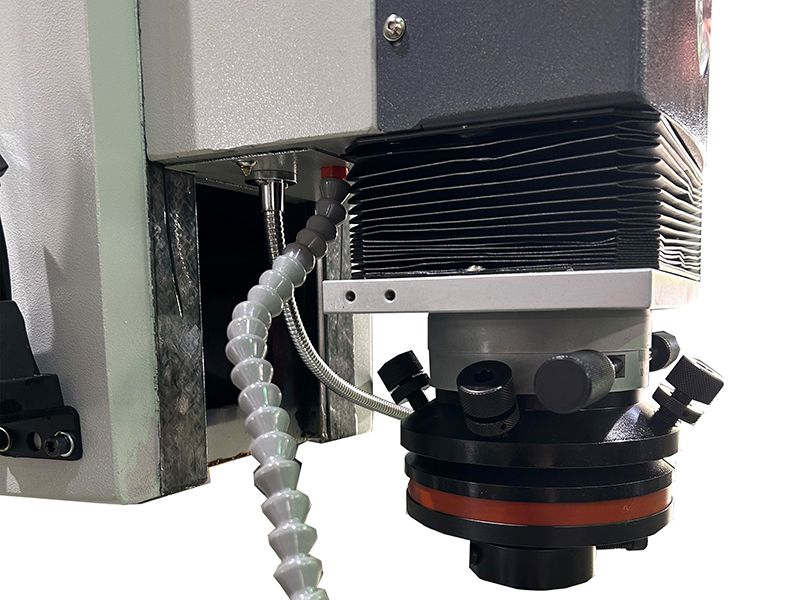
- The Z-axis is equipped with a linear guide and high-precision ball screw, a structural design that ensures the stability and accuracy of Z-axis movement. The linear guide provides a smooth motion path, while the high-precision screw guarantees precise movement of the Z-axis, thereby ensuring the accuracy and stability of the machine while manufacturing. This structure, combined with a PWM servo system (equivalent to CNC grade), delivers maximum operational efficiency. The PWM (Pulse Width Modulation) servo system can precisely control the speed and position of the motor, providing more accurate motion control, which allows the EDM machine to achieve high efficiency during the machining process.
- The Z-axis also features an additional electric auxiliary stroke. This ensures that the Z-axis can perform precise vertical movements through the linear guide and high-precision screw and furthermore extend the Z-axis movement range and flexibility further through the electric auxiliary stroke. This electric auxiliary stroke can provide additional movement support when needed, helping the EDM machine adapt to different machining requirements, thus enhancing the versatility and flexibility of the machining process.
Controller Performance and Features
● Automatic Indexing: The system allows users to directly select the material and area to be machined. After inputting the machining depth and starting height, the system automatically searches for the optimal conditions and generates the machining program. Users can also edit and save this machining program, which can be reloaded for use in future operations without altering the original database content.
● High-Efficiency Discharge Module: The discharge circuit uses MOSFET transistors and is equipped with a fast discharge device (POWER SINK) to improve machining efficiency and reduce electrode wear. The machining circuit employs FPGA IC components, enabling faster monitoring of the discharge state (capable of single discharge waveform monitoring), which is more effective in preventing carbon buildup (ARC). It also provides users with the ability to set ARC voltage levels, ARC time, and ARC sensitivity to improve machining efficiency more effectively.
Additionally, it offers two-stage gap (GAP) and two-stage pause (OFF TIME) functions to assist users by automatically adjusting machining parameters to the two-stage function when any ARC condition occurs during machining, thus achieving better machining efficiency.
These design features and functions are all aimed at enhancing machining efficiency, reducing wear, and providing better operability and stability.
● Servo Control: The servo control system uses DSP digital processing, providing faster response times, with feedback loop control up to every 0.2 ms, which is faster than the typical response time of over 1 ms for general PC-based controllers. This characteristic enhances the stability of the spindle during machining, ensuring smoother machine operation.
The ZNC EDM machine also offers a multi-stage debris removal mode, which is useful for deep hole machining and thin plate machining, providing more flexible machining options. Furthermore, the servo protection function is a crucial feature that prevents electrode damage due to improper user operation, ensuring the safety and longevity of the electrode during the machining process.
These features make the ZNC EDM machine's servo control more flexible, stable, and safe, capable of handling various machining demands while ensuring high-quality machining results.
● Multiple Machining Parameters: The system can store up to 50 files, each containing 200 sets of machining parameter tables for saving machining conditions.
Product Specification
Technical Spec. | |||
---|---|---|---|
Mechanical Structure | Moving Table | Distance Between Platen to Table | 640mm |
Work Tank Capacity L x W x H (mm) | 1100 x 600 x 400mm | Optical Scale Display | 5um |
Work Table Size | 700 x 400mm | Max. Machining Current | 60A 90A (Optional) |
X Axis Travel (Right-Left) | 400mm | ||
Y Axis Travel (Front-Back) | 300mm | Min. Electrode Wear Ratio | 0.15% |
Z Axis Travel | 180mm | Machine Weight | 1800kgs |
Auxiliary Axis Travel | 250mm | Fluid Tank Capacity | 350L |
Max. Workpiece Weight | 1500kgs | Machine Outside Dimensions (W x D x H) | 2500 x 1500 x 2250mm |
Max. Electrode Weight | 100kgs |
- Gallery
- Machining conditions and depth input are displayed on a single screen, allowing users to grasp the information immediately.
- The AI automatic indexing function allows users to directly select the material and area to be machined. After inputting the machining depth and starting height, the system automatically searches for the optimal conditions.
- The one-page multifunctional calibration includes edge finding, inner hole finding, outer circle finding, vertex finding, and circle center finding.
- When the fire sensor detects flames, it sends an alarm signal and pauses the machine to prevent a fire from occurring.
- When the worktable catches fire due to excessive oil temperature, the fire extinguisher is activated to extinguish the fire, providing a second layer of protection beyond the fire sensor.
- The adjustable electrode head allows for quick electrode replacement and adjustments for parallelism and verticality.
- The three-jaw chuck allows dielectric fluid to pass directly through the jaws and flow along the electrode into the mold, enhancing debris removal efficiency.
- The vertical filter cartridge design makes it easy to replace the filter and prevents the filter from breaking during replacement, avoiding spills of oil and metal debris.
- Video
How can small mold manufacturers achieve high precision without investing in expensive large EDM machines?
The EB606N's T-shaped high-rigidity structure specifically addresses this challenge by ensuring every machining point on the worktable moves within the center of the machine's base, achieving optimal precision even with a smaller footprint. Combined with Meehanite cast iron construction and stress-relieved heat treatment, this economical ZNC EDM delivers large-machine precision at a fraction of the investment cost, making it ideal for small to medium mold manufacturers looking to enhance capabilities without overextending their budget.
Equipped with advanced control technology, the EB606N offers AI automatic indexing for optimal machining conditions, a high-efficiency MOSFET discharge module with FPGA IC components for fast discharge state monitoring, and DSP digital processing for superior servo control. The user-friendly interface displays machining conditions and depth input on a single screen, significantly reducing the learning curve for operators. With versatile applications including mold core machining, oil extraction pipe production, and brand logo mold creation, the EB606N provides manufacturing facilities with a reliable, accurate, and cost-effective EDM solution that maintains JSEDM's commitment to precision and quality.