JSEDM Wire Cut EDM: High-Precision Submerge & Flush-Type Electrical Discharge Machines
JSEDM offers advanced Wire Cut EDM machines in both Submerge-Type and Flush-Type configurations. Our high-precision electrical discharge machines deliver micron-level accuracy, 5-axis simultaneous operation, and superior performance on hard materials like steel and titanium alloys. Ideal for precision mold manufacturing, aerospace components, and complex industrial applications.
Wire Cut EDM
Also known as Slow-Feeding Wire Cut EDM. Unlike medium and fast-feeding wire EDM, slow-feeding wire EDM is mainly used for cutting high-precision workpieces. It is characterized by fast cutting speed, dust-free operation, and recyclable consumables
Wire Cut Electrical Discharge Machining (Wire Cut EDM), also known as slow-feeding wire EDM in China, is a metal processing machine aim for precise and high-tech processing. There are two main types of Wire EDM: Submerge-Type and Flushing-Type.
Submerge-Type Wire EDM maintains a stable cutting temperature in water and effectively filters out iron filings and impurities after cutting, making it a versatile machine for high-precision workpieces.
Flushing-Type Wire EDM is an economical model. Under certain conditions, its cutting performance is similar to submerge-type. However, outside these conditions, cutting speed needs to be reduced based on material thickness and material type to avoid frequent wire breaks.
Unlike traditional turning and milling processes, Wire Cut Electrical Discharge Machining (Slow-Feeding EDM) has several unique characteristics. Firstly, Wire EDM can achieve extremely high machining precision, typically to micron level. This makes it particularly suitable for manufacturing components requiring exceptional accuracy, such as gear for watches and stamping dies.
Unlike traditional machining methods, Wire Cut EDM is not limited by the hardness of the workpiece. It can easily cut high-hardness materials like steel and titanium alloys simply using a thin copper wire.
Additionally, Wire Cut EDM features 5-axis simultaneous operation (4-axis during machining) that allows for efficient cutting of complex shapes, such as tapered or asymmetrical forms, without the need for special tools.
Furthermore, Wire Cut EDM has the advantage of low machining side effects. Since the cutting process does not involve direct contact with the workpiece itself, there will be no tool wear or vibration that might occur while performing traditional machining methods.
Working Principle of Wire Electrical Discharge Machine:
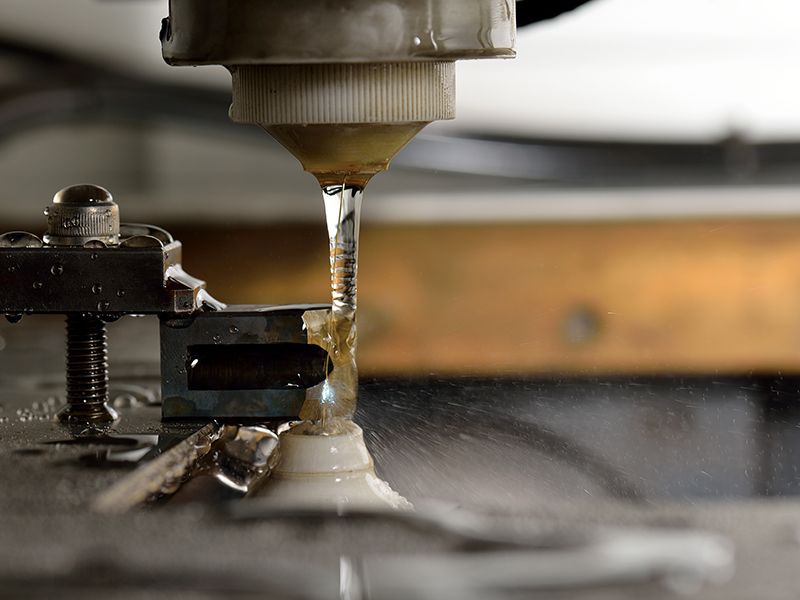
- Electrode: The electrode in Wire EDM is equivalent to the cutting tool in traditional machining, using a very thin copper wire as the conductive (cutting) medium. The diameter of this wire is very thin, usually between 0.1mm and 0.3mm.
- Discharge Process: There is a tiny gap between the workpiece and the electrode. By applying voltage in this gap, electrical sparks are generated. These sparks are conducted from the electrode (copper wire) to the workpiece, heating the material to a high temperature.
- Material Removal: High temperature causes the workpiece to melt and oxidize, forming tiny holes. The electrode (copper wire) passes through these holes while maintaining a stable gap between the workpiece and the electrode (copper wire) to ensure a continuous discharge process. In this way, the electrode (copper wire) can gradually cut out the desired shape.
- Work File: The cutting process is controlled by a CNC (Computer Numerical Control) system. Engineers can create a 3D model of the part using CAD (Computer-Aided Design) software and then convert these models into CNC instructions to guide the Wire EDM machine to complete the cutting.
How Can 5-Axis Wire EDM Technology Revolutionize Your Die Manufacturing Process?
Our 5-axis Wire EDM systems enable precision mold and die manufacturers to achieve complex geometries with micron-level accuracy in a single setup. Unlike traditional machining methods, JSEDM's technology works regardless of material hardness, eliminating the need for multiple processes and reducing production time by up to 40%. Contact us to discover how our Wire EDM solutions can enhance your die manufacturing capabilities while reducing overall production costs.
Our Wire Cut EDM machines feature advanced 5-axis simultaneous operation capability, allowing for the efficient production of complex shapes and tapered forms without specialized tooling. The Submerge-Type models maintain stable cutting temperatures in water and effectively filter impurities, ensuring consistent results for the most demanding applications. For more economical solutions, our Flush-Type EDM machines deliver comparable performance under specific conditions while offering an excellent price-to-performance ratio. All JSEDM machines are backed by our 40+ years of industry expertise and comprehensive global support network.