JSEDM Wi-530S: High-Precision Submerge-Type Wire Cut EDM with 500/300/300mm XYZ Travel
JSEDM Wi-530S Submerge-Type Wire Cut EDM delivers exceptional precision with 500/300/300mm XYZ travel capability. Featuring high-rigidity structure, advanced 5-axis AC servo system, and 15-inch touchscreen interface. Ideal for mold manufacturing, tooling, and precision parts production with 700kg workpiece capacity and ±22.5° taper angle capability.
Submerge-Type Wire Cut EDM XYZ Travel 500 / 300 / 300
Wi-530S
Submerge-Type Slow Feeding Wire Cut EDM
The Wi-530S and Wi-430S submerged wire-cut EDM machines are structurally similar, but the Wi-530S offers enhancements in some key specifications, such as travel range, load capacity, and table size. This means that the Wi-530S has a broader processing range and can handle larger and more complex workpieces.
Additionally, both machines use the same components, such as C2-grade screws and SP-grade linear guides from PMI, as well as drive controllers and servo motors made by Delta Electronics. The selection of these components ensures consistency in precision, stability, and durability between the two machines.
Machine Introduction
The Wi-530S has a maximum workpiece placement size of 870 x 540 x 295mm and a maximum load capacity of 700kgs, making it suitable for handling larger metal parts or molds.
Additionally, it offers an X-axis travel of 500mm, a Y-axis travel of 300mm, a Z-axis travel of 300mm, a U-axis travel of 100mm, and a V-axis travel of 100mm.
In practical applications, the Wi-530S has a larger processing range and capability compared to the Wi-430S, enabling it to handle larger and more complex workpieces.
Depending on the size of the customer's molds and workpieces, as well as the required processing range, the Wi-530S is more capable of processing the following four types of industry applications:
- Mold Manufacturing: This machine has significant potential in mold manufacturing. It can produce complex-shaped molds, such as plastic molds and metal molds. Due to its high precision and multi-axis movement features, it can create high-quality molds.
- Tooling: In industrial design and manufacturing, various tools are needed for testing and inspection. This machine can produce precise tools to support product development and production.
- Automotive Parts Manufacturing: Automotive parts typically have complex shapes and require high precision. This machine can be used to manufacture automotive engine components, suspension system parts, and more.
- Aerospace Parts: The aerospace industry demands high precision and durability for its parts. This machine can produce parts that meet aerospace standards, such as engine components and fuselage parts.
High-Rigidity Structure:
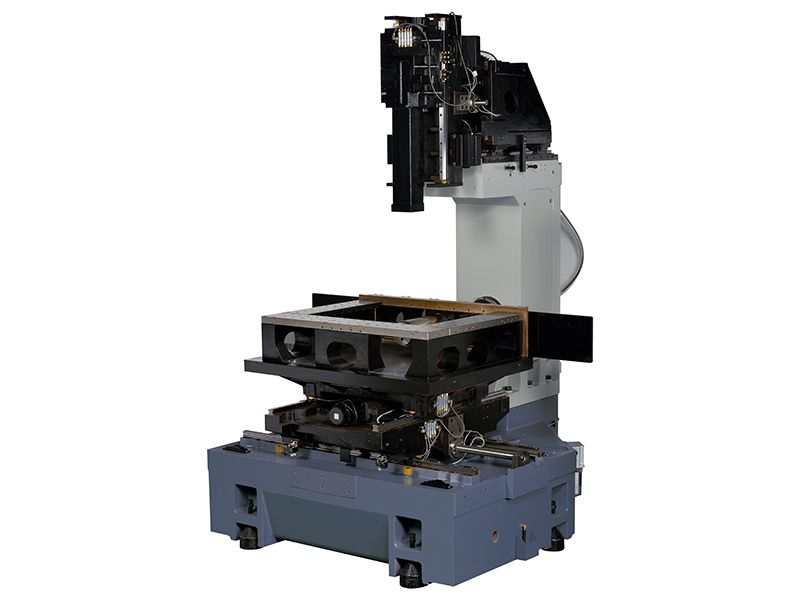
- The machine body utilizes CAE (Computer-Aided Engineering) to simulate structural deformation of each axis during actual operation. Therefore, we use a high-rigidity T-shaped machine body structure to reduce load and thermal deformation issues, ensuring permanent mechanical accuracy.
- Casting was made from Meehanite cast iron, stress-relieved through heat treatment, it features a high-rigidity, symmetrically balanced design to reduce load and thermal deformation.
- The overall transmission structure employs a high-power AC (400W) servo motor, paired with Taiwan's PMI ballscrew and linear guides, this combination greatly reduces rotational errors. And with the adjustment of pitch compensation and backlash compensation in the control system, it ensures the precision of the machine's movement.
High-Precision Drive Shaft System:
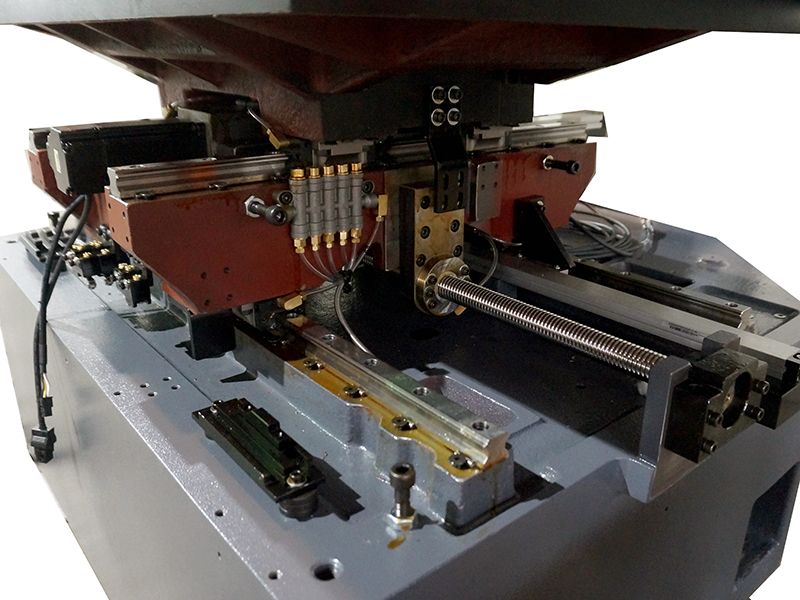
The drive shaft uses highly precise "double nut" ball screws to achieve high rigidity, smooth operation, and minimal lead error. It is equipped with a high-torque, high-response AC (400W) servo motor, with an optional Fagor high-resolution optical scale for full closed-loop control. The optical scales are installed as close to the ball screws as possible, ensuring each axis maintains high precision, long life, and excellent stability.
Self-developed Wire Delivery System:
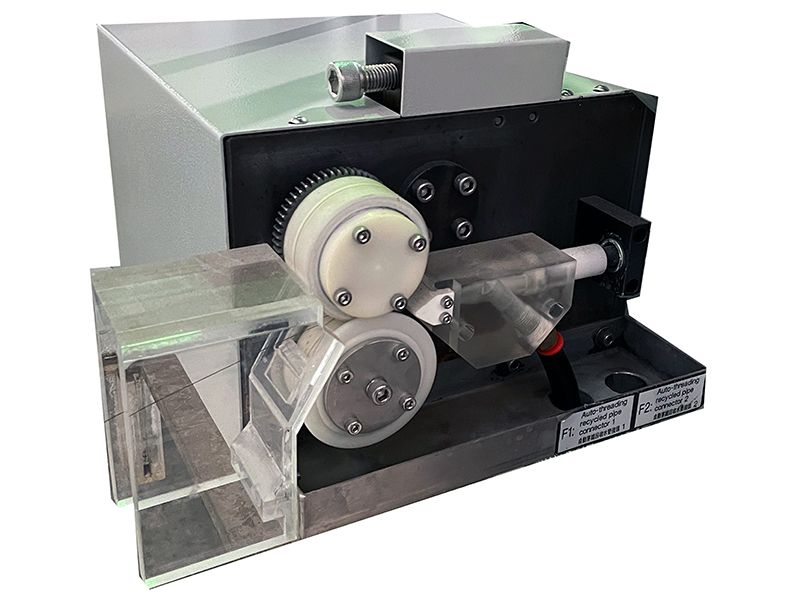
- The special structural design, combine with high-hardness ceramic pully, results in less wear and longer lifespan.
- With Japanese Panasonic AC servo motors, magnetic powder clutches, wire collection motors, and wire clamping mechanisms, the system can accurately make adjustment for instability caused by wire vibrations, ensuring stable wire delivery and low failure rates.
- The wire delivery system uses advanced constant tension motors for copper wire, it assures tension stability at all times and prevent copper wire entanglement caused by sudden breaks during normal operation.
- The wire delivery section utilizes a conduit-style collection structure. During threading, high-pressure fluid flow guides the copper wire to complete the threading process quickly within 3-5 seconds. Additionally, the use of high-quality ceramic wheel mechanisms ensures minimal wear over long-term use, eliminating the need for additional parts. Even ∅0.1mm copper wire can pass through easily without tangling.
Controller Performance and Features
● Right-angle Compensation: This function compensates the right-angle and parallelism of the XY and UV planes of the wire cutting machine. After compensation, the machine's right-angle accuracy can reach within ±1.5μm/300mm.
● Five Types of Corner Assist Lines: Contains additional corner assist line functions compared to other wire cutting machines:
0 - Intersection point
1 - <90 degrees (tangent) => Additional function
2 - <90 degrees (arc) => Additional function
3 - Tangent => Additional function
4 - Arc => Additional function
● Fuzzy G95 Control: Achieves more than 95% of manual operation speed, or even better.
● 212 Sets of Ultra-fine Machining Parameters: Provide 212 sets of ultra-fine machining parameters that can be adjusted according to different cutting needs.
● 10 Sets of Arc Deceleration Machining Parameters: Automatically switches machining parameters according to the arc radius set by the user.
● 10 Sets of Corner Deceleration Machining Parameters: Automatically switches machining parameters according to the corner angle set by the user.
● Ethernet Access Interface: Provides an Ethernet interface for accessing large amounts of machining data.
● 100 Sets of Coordinate System Records (Including G54 ~ G59): Traditional wire cutting systems only provide 6 sets of coordinate records (G54 ~ G59). JSEDM Wire Cutting System offers up to 100 sets of coordinate system records, which can be used for positioning movements.
● Dynamic 3D Graphical Display: Simulates graphics in 3D and allows zooming, regional enlargement, and rotation for detailed viewing.
● Touch Operation Interface: Uses a 15-inch high-resolution industrial-grade touch screen with an intuitive interface, significantly reducing operator learning time.
● Simple Operation Interface: Compared to the traditional DOS multi-layer operation menu, the Wire Cutting System simplifies the operation interface significantly and adds a hotkey area to centralize commonly used function keys, effectively reducing learning time and operation difficulty.
● Simplified Calibration Steps: Most functions only require 2-3 steps to start the calibration process, this simplifies the operation flow and shortening calibration time.
● Maintenance Information: Records six types of maintenance information, timely reminding the operator to replace consumables. The maintenance information includes: 1. Copper wire usage length, 2. Waste wire bucket usage time, 3. Water tank filter usage time, 4. Electron feeder usage time, 5. Ion exchange resin usage time, 6. Workbench usage time.
● POS Function: When this function is activated during machining, it automatically speeds up the machine when the workpiece is not in its path and resumes the machining speed once it touches the workpiece and cutting starts. This function greatly reduces machining time.
Product Specification
Technical Spec. | |||
---|---|---|---|
Machine Type | Submerge | Drivetrain | 5 axis AC servo system |
Mechanical Structure | Three-Body Independent | Simulations Axis | XYUV (4 Axis) |
Max. Workpiece Size L x W x H (mm) | 870 x 540 x 295mm | Wire Diameter Range | Φ 0.10 ~ 0.3mm |
Max. Workpiece Weight | 700kgs | Max. Taper Angle | ± 22.5° (Thickness 100mm) |
X Axis Travel (Right-Left) | 500mm | Max. Axis Load | 6kgs |
Y Axis Travel (Front-Back) | 300mm | Conductivity | Automatic |
Z Axis Travel | 300mm | Water Tank Capacity | 570L |
U Axis Travel | 100mm | Dimension (W x D x H) | 3250 x 2200 x 2150mm |
V Axis Travel | 100mm |
- Gallery
- 2.5D image simulation allows customers to easily track the current cutting status, especially in taper cutting and abnormal shape with upper-lower shape difference.
- Multi-functional calibration interface equipped with graphical explanations, making it easy for users to learn and operate.
- Time-based maintenance records enable customers to replace consumables at routine time, enhancing machining stability.
- Time-based maintenance records enable customers to replace consumables at routine time, enhancing machining stability.
- With machining parameter data sheet, customers can refer to built-in parameters and select suitable machining conditions based on wire diameter, number of machining passes, and material type.
How Does the Wi-530S's ±22.5° Taper Capability Address Critical Aerospace Component Challenges?
Aerospace components often require complex angular features that must meet stringent tolerance requirements. The Wi-530S excels in this domain with its exceptional ±22.5° taper cutting capability (for workpieces up to 100mm thick), combined with the 2.5D image simulation system that provides real-time visualization of taper cutting progress. This allows aerospace manufacturers to produce critical components with complex geometries in a single setup, eliminating the alignment errors and additional handling associated with multiple setups. The machine's high-precision drive shaft system with double-nut ball screws ensures that these angular features maintain the micron-level accuracy demanded by aerospace industry standards, while reducing production time and costs.
What distinguishes the Wi-530S is its comprehensive performance package combining mechanical excellence with intelligent control. The 5-axis AC servo system works in harmony with PMI C2-grade ball screws and SP-grade linear guides to ensure positioning accuracy and smooth operation. The advanced controller features 212 sets of ultra-fine machining parameters, dynamic 3D graphical display, and intelligent corner/arc deceleration functions through a user-friendly 15-inch touchscreen interface. This makes the Wi-530S ideal for demanding applications in mold manufacturing, tooling production, automotive components, and aerospace parts where precision, efficiency, and reliability are paramount.