JSEDM CNC-EB1880L: Column Moving-Type CNC EDM Machine with 1800/800/600mm XYZ Travel
JSEDM CNC-EB1880L: Advanced column moving-type CNC EDM machine with 1800/800/600mm XYZ travel designed for medium to large mold manufacturing. Features high-rigidity structure, precision spindle, and AI automatic indexing for superior machining accuracy. Capable of handling workpieces up to 7000kg with minimal electrode wear ratio of 0.12%.
Column Moving-Type CNC EDM XYZ Travel 1800 / 800 / 600
CNC-EB1880L
Column Moving-Type CNC Electrical Discharge Machine
The EB1880L boasts several impressive features. Firstly, its moving column structure ensures stability and precision during the machining process, allowing the machine to withstand higher machining loads. Its XYZ-axis travel is extensive, enabling it to handle workpieces of various sizes, and the large worktable provides ample machining space. Additionally, the EB1880L is equipped with advanced components, such as a high-precision servo system that guarantees machining efficiency and accuracy. Like other models, the EB1880L can also be equipped with an automatic tool changer and a C-axis, making it a powerful, stable, and reliable EDM machine capable of meeting the demands of various industrial applications while ensuring product quality and efficiency.
Machine Introduction
The CNC-EB1880L is a top-tier electrical discharge machine, offering exceptional performance and features. Its XYZ-axis travel measures 1800mm (X-axis), 800mm (Y-axis), and 600mm (Z-axis), with a worktable size of 1850 x 1000mm, providing ample machining space suitable for handling workpieces of various sizes. The machine adopts a moving column structure, ensuring stability and precision during the machining process, enabling the CNC-EB1880L to tackle a wide range of complex machining tasks. This model is equipped with advanced components that ensure high-efficiency and high-precision machining, making it an ideal choice for modern manufacturing.
The EB1880L has a wide range of applications, below are several examples:
- Wire Winding Drums: These molds are typically large and have an external grid structure that requires machining through electrical discharge. The EB1880L, with its spacious machining area and moving column structure, can handle molds of various sizes, achieving high-efficiency and precision in winding processing, thereby meeting the demands of the wire manufacturing industry.
- British Brand Vacuum Cleaners: The vacuum cleaner's casing, internal structure, and various components often require high-precision machining to ensure product performance and quality. The EB1880L, with its advanced moving column structure and efficient machining capabilities, can achieve the machining of complex shapes, meeting the vacuum cleaner manufacturers' requirements for precision and efficiency.
- Japanese Dehumidifiers: The casing, internal structure, and drainage system components of dehumidifiers require precise machining to ensure the performance and stability of the dehumidifier. The EB1880L, with its large machining space and high-efficiency capabilities, can handle molds of various shapes and sizes, achieving high-precision and high-efficiency machining, thus meeting the needs of dehumidifier manufacturers.
High-Rigidity Structure:
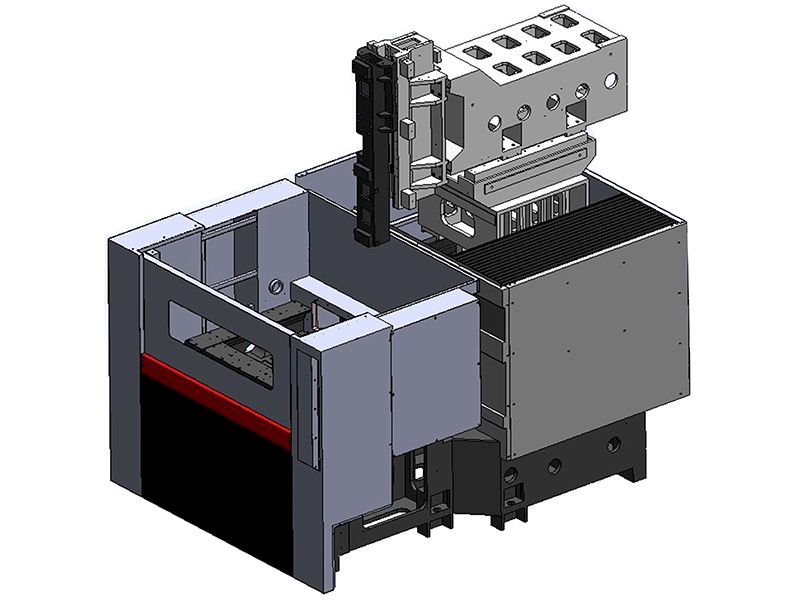
- The machine adopts a high-rigidity moving column structure capable of supporting workpieces up to 7000 kgs, reducing issues related to machine load and thermal deformation, thereby ensuring long-term precision.
- Made from Meehanite cast iron, the machine undergoes stress-relief heat treatment, providing a high-rigidity, symmetrically balanced base design. The worktable is heat-treated and precision-ground, making it wear-resistant and maintaining flatness even under heavy loads.
- The base design utilizes a moving column (bullhead type) structure, ensuring that the flatness of the workpiece on the table is not affected during movement, delivering optimal working precision. The robust base design prevents deformation even when subjected to long-term heavy loads.
Wide Linear Guide Span and Precision Ball Screw:
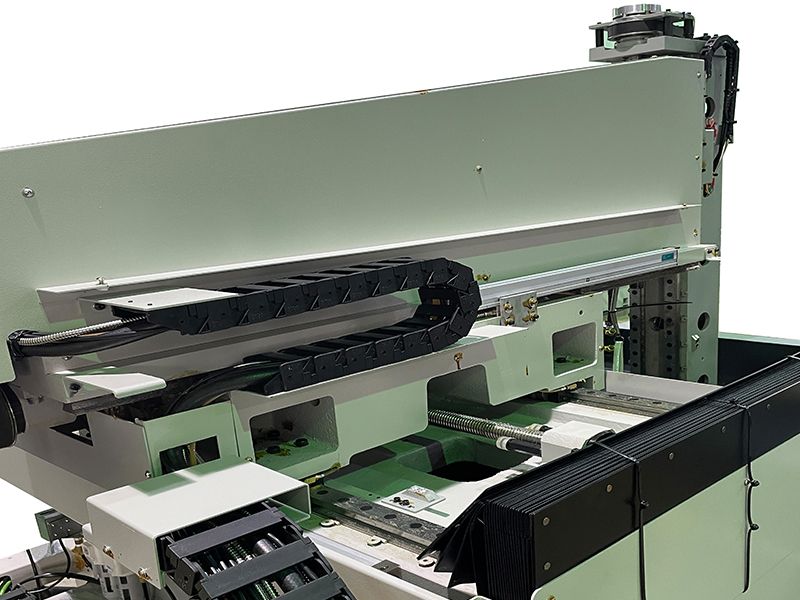
- The X and Y axes utilize low-friction linear guides, ensuring machine precision and smooth operation during its movement. The wide linear guide and span ensure accurate positioning and feed data during long-term back-and-forth and side-to-side movements, especially during reaming and vector machining, maintaining the machine's precision (backlash value) over time.
- The X-axis linear guide (Ψ 30mm) is mounted on the machine's middle base, ensuring flatness during installation and extending the lifespan of the guide, thereby maintaining machine accuracy.
- The Y-axis linear guide (Ψ 30mm) is installed on the machine's upper base, ensuring flatness during installation and lightness (without bearing weight) to reduce friction and extend the lifespan, thus permanently ensuring machine accuracy.
- The X-axis (Ψ 32mm) and Y-axis (Ψ 32mm) utilize precision-grade ball screws combined with low-friction linear guides to ensure machine accuracy.
Precision Spindle:
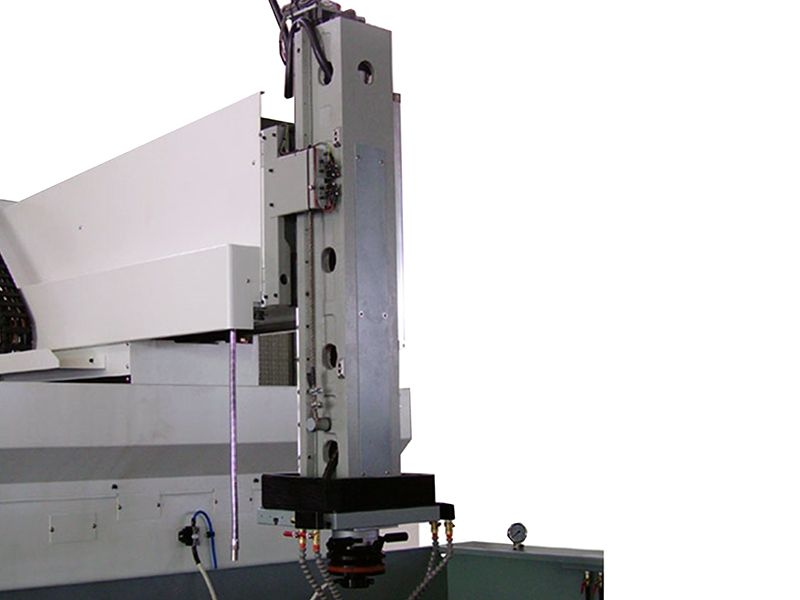
- The spindle section features an integrally cast design to ensure stability during large electrode machining. It also utilizes alloy steel guides (Ψ 30mm) combined with roller bearings, minimizing friction and ensuring spindle feed accuracy.
- The spindle tower is equipped with a 400W servo motor, making the spindle operation more lightweight (without counterweights) while ensuring precise displacement during operation and extending the lifespan of the ball screw (Ψ 25mm).
C-axis Features and Applications:
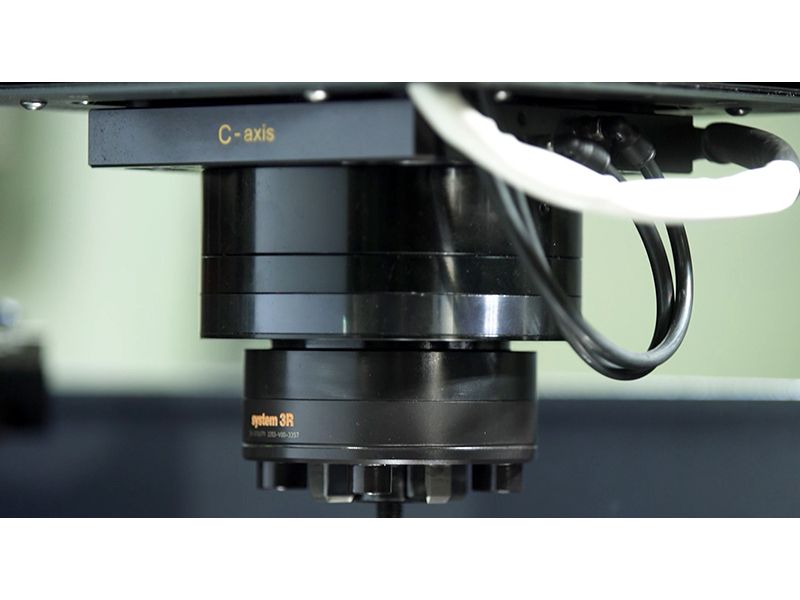
- The C-axis offers high-precision positioning capability, allowing for accurate positioning and rotation of parts during machining. This enables more precise machining and better results when working on parts that require rotational machining.
- The C-axis can perform indexing machining, which involves machining at fixed angles. This is particularly useful for parts requiring periodic or repetitive machining, improving consistency and efficiency.
- For parts with complex thread structures, the C-axis can facilitate thread machining. These thread structures may have unique shapes that require machining at various angles, and the rotational function of the C-axis allows for precise thread machining.
Automatic Tool Changer (ATC) and the Advantages of Automation:

- Allows quick and precise tool changes, reduces tool change time and thereby increasing machining efficiency.
- Ensure that it is precise in every tool change, avoiding errors caused by human factors, which in turn improves machining accuracy.
- Can automatically complete tool changes during the machining process, reducing downtime and increasing machine uptime.
- Minimizes the need for manual intervention, reducing labor requirements while also lowering the risk of errors and accidents caused by human operation.
Controller Performance and Features
● Automatic Indexing: The system allows users to directly select material type and area, input machining depth and starting height, and then automatically search for the optimal conditions to generate the machining program. Users can also edit and save the generated program, which can be reloaded for future use without altering the original database content.
● High-Efficiency Discharge Module: The discharge circuit uses MOSFET transistors and a fast discharge device (POWER SINK) to enhance machining efficiency and reduce electrode wear. The machining circuit employs FPGA IC components for faster monitoring of discharge conditions (up to single discharge waveform monitoring), providing more effective prevention of carbon buildup (ARC). Users can set ARC voltage levels, ARC time, and ARC sensitivity to further improve machining efficiency. Additionally, it offers two-stage gap and two-stage off-time functions to assist users in automatically adjusting machining parameters when ARC occurs, leading to better machining efficiency. These features and designs aim to improve machining efficiency, reduce wear, and provide better operability and stability.
● Servo Control: The servo control system uses DSP digital processing, allowing for faster response times, with loop control occurring every 0.2ms, which is faster than the typical 1ms or more response time of PC-based controllers. This characteristic enhances spindle stability during machining, ensuring smoother machine operation.
Additionally, the CNC EDM machine offers a multi-stage debris removal mode, suitable for deep hole machining and thin sheet processing, providing more flexible machining options. Moreover, the servo protection function is an important feature that prevents electrode damage caused by improper user operation, such as mold crushing. This protection function ensures the safety and longevity of the electrode during the machining process.
These combined features make the CNC EDM machine's servo control more flexible, stable, and safe, capable of meeting various machining demands while ensuring high-quality machining results.
Product Specification
Technical Spec. | |||
---|---|---|---|
Mechanical Structure | Column Moving-Type | Distance Between Platen to Table | 1050mm |
Work Tank Capacity L x W x H (mm) | 2600 x 1320 x 700mm | Optical Scale Display | 1um |
Work Table Size | 1850 x 1000mm | Max. Machining Current | 60A 90A (Optional) |
X Axis Travel (Right-Left) | 1800mm | ||
Y Axis Travel (Front-Back) | 800mm | Min. Electrode Wear Ratio | 0.12% |
Z Axis Travel | 600mm | Machine Weight | 9000kgs |
Max. Workpiece Weight | 7000kgs | Fluid Tank Capacity | 2800L |
Max. Electrode Weight | 500kgs | Machine Outside Dimensions (W x D x H) | 5000 x 4000 x 3200mm |
- Gallery
How Can the EB1880L's Moving Column Structure Improve Your Large Mold Production Efficiency?
The EB1880L's moving column design provides unmatched stability for machining large molds, supporting workpieces up to 7000kg while maintaining precision. Unlike fixed-column machines, this structure ensures the worktable doesn't deviate from the center point, preserving flatness during machining operations. Our Meehanite cast iron construction with stress-relief heat treatment minimizes thermal deformation, allowing continuous operation on complex, heavy molds without sacrificing accuracy—resulting in up to 30% higher production efficiency for large-scale mold manufacturing.
What truly distinguishes the CNC-EB1880L is its advanced control system featuring AI automatic indexing, high-efficiency discharge modules with MOSFET transistors, and sophisticated servo control with 0.2ms response time. The machine can be enhanced with an automatic tool changer (ATC) and C-axis functionality for complex thread structures and indexed machining operations. Safety features include integrated fire sensors and extinguishers, while the vertical filter cartridge design simplifies maintenance. With a minimal electrode wear ratio of just 0.12% and specialized machining capabilities for applications ranging from wire winding drums to precision components for vacuum cleaners and dehumidifiers, the CNC-EB1880L delivers exceptional performance, reliability, and cost-efficiency for demanding manufacturing environments.